Singular Focus, Purpose-Built Solutions: Your Partner in Life Science Insurance
Berkley Life Sciences is solely dedicated to providing premiere insurance coverage for today’s top life sciences companies.
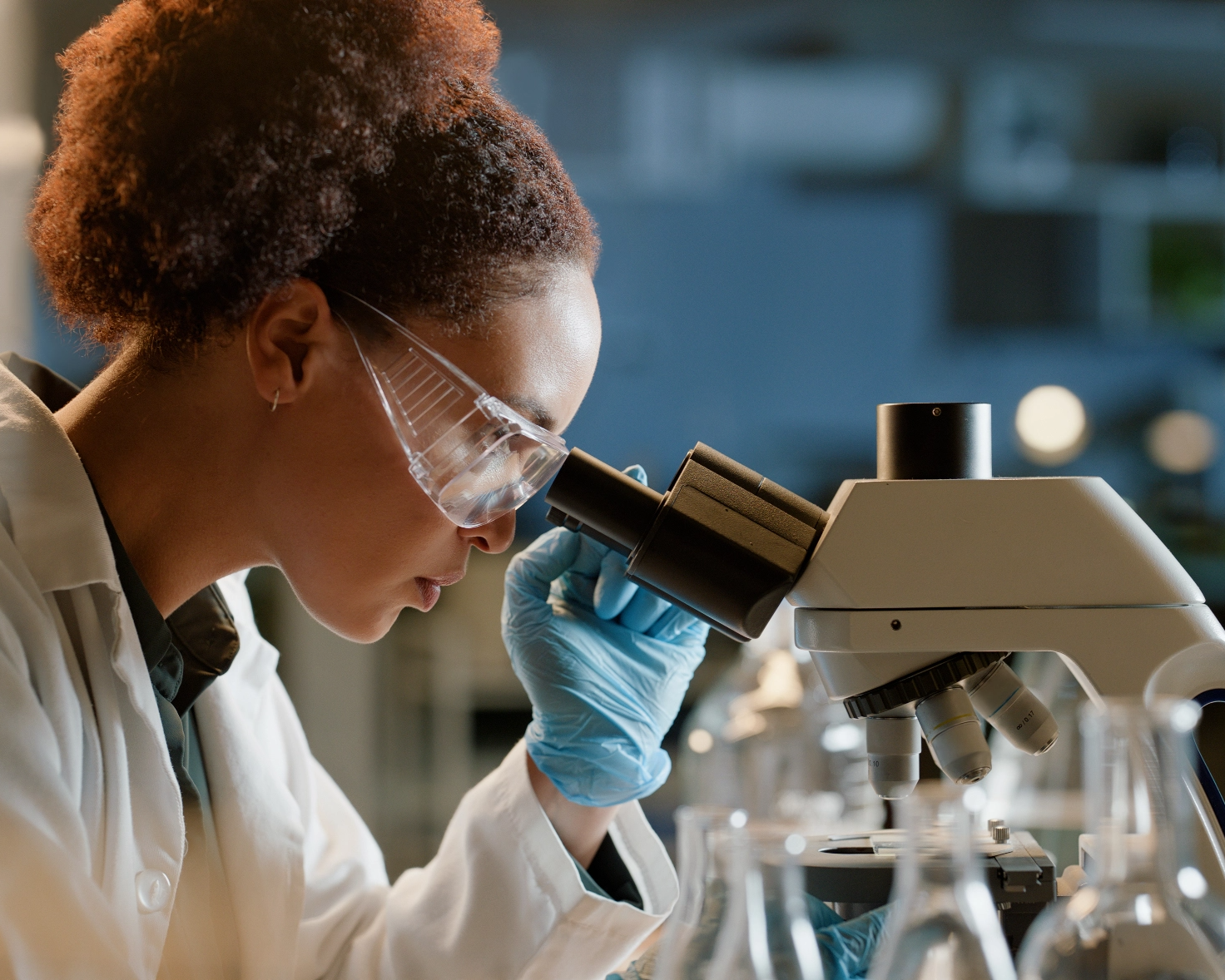
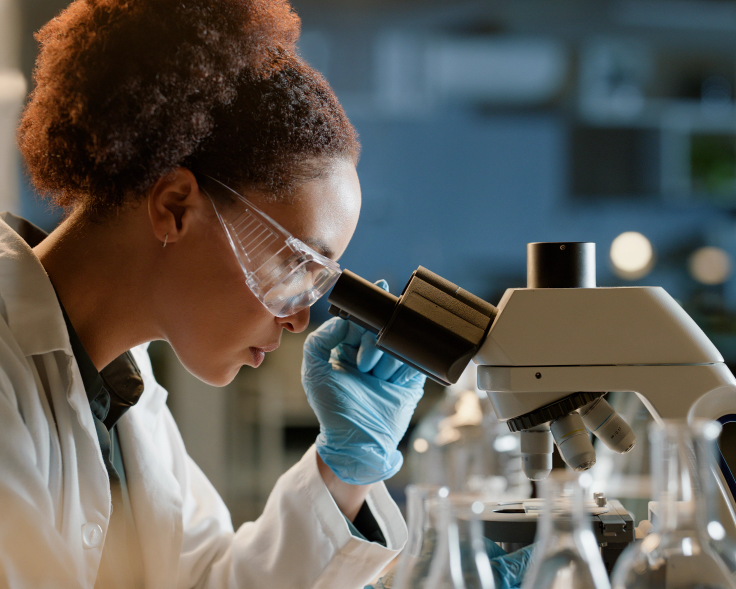
Life Science Insurance Protecting Tomorrow’s Innovations
Comprehensive. Customized. Multinational. We provide property and casualty insurance products and services tailored to life science businesses globally. Our approach is collaborative, with underwriting, in-house claims, and risk management working in tandem to provide a complete and specialized insurance solution.
-
Berkley Life Sciences underwriters strategically partner with our agents and brokers on defined risk types so we can deliver appropriate solutions -- when other carriers might dismiss a risk because it doesn't "fit the box."
-
All submissions are handled within Berkley Life Sciences' authority without the influence of a multi-industry home office team, resulting in a hit ratio typically greater than 50% over the past 4 years.
-
Berkley Life Sciences' collaborative underwriting approach includes swift access to an internal team of seasoned claims, legal and risk management professionals who work directly with agents and insureds to help find innovative solutions to even the most challenging account issues.
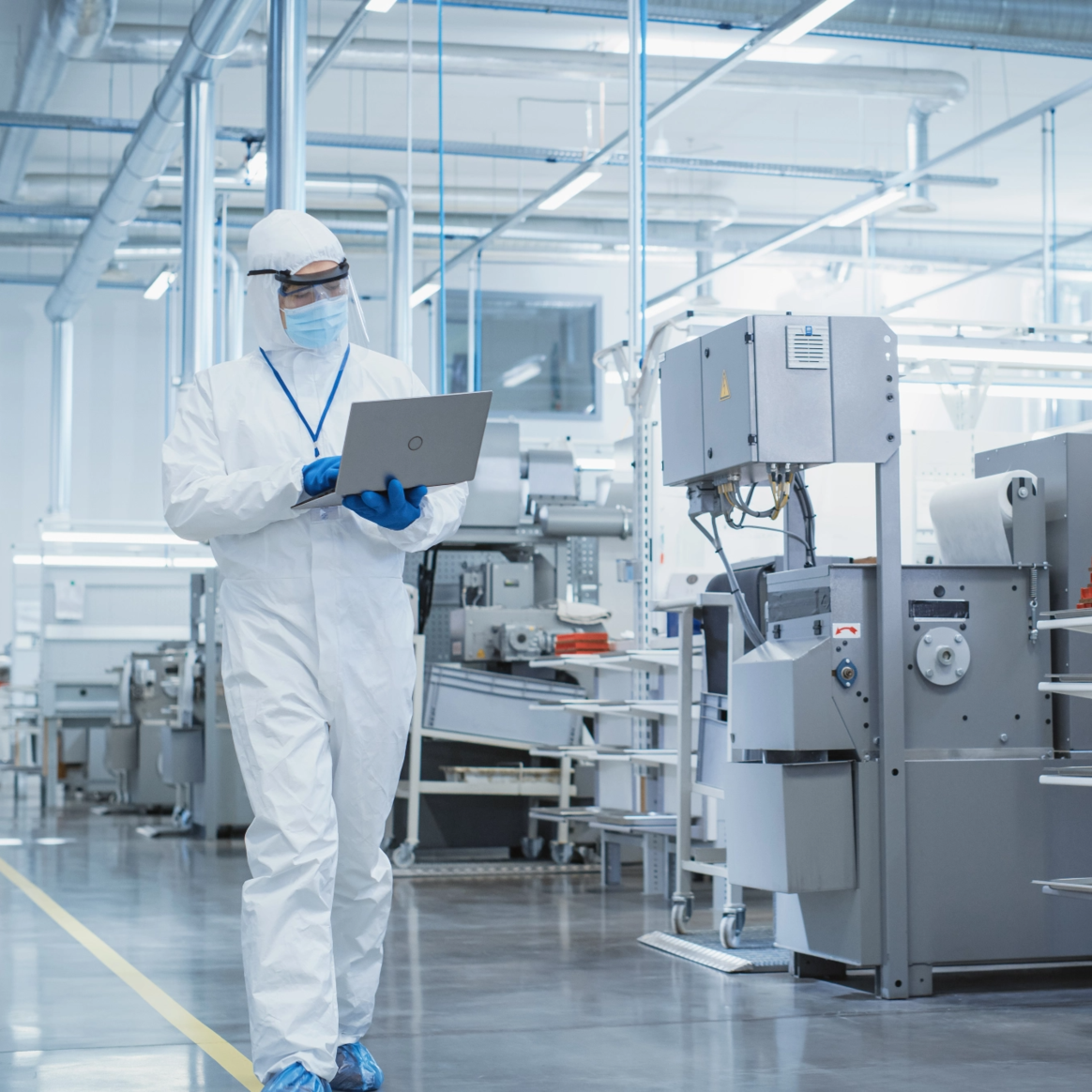
In-House Claims
From the start of the underwriting process, our in-house claims team is a true partner in your insurance experience. With extensive life science products liability claim and litigation expertise, our claims team collaborates with insureds, brokers, and our defense counsel to actively lead claims to just resolution.
The Power of Berkley
Berkley Life Sciences is one of the 55+ (re)insurance businesses worldwide that comprise the Berkley brand. Berkley is one of America’s largest commercial lines property casualty insurance providers, operating worldwide within two segments of the P&C insurance business: Insurance and Reinsurance & Monoline Excess. Each business offers expertise within an industry, product, or region.
Berkley Life Sciences is a member of W. R. Berkley Corporation, a Fortune 500 company listed on the New York Stock Exchange and is part of the S&P 500. W. R. Berkley Corporation’s insurance company subsidiaries are rated A+ (Superior), Financial Size Category XV by A.M. Best Company and A+ (Strong) by Standard & Poor’s.
Berkley’s competitive advantage lies in its long-term strategy of decentralized operations. This structure provides each Berkley business the agility of a small business—the ability to identify and respond quickly and effectively to changing market conditions and local customer needs. It provides our Berkley businesses with the strength and resources of a Fortune 500 organization as well as the financial accountability and incentives to attract and retain the highest-caliber professionals.
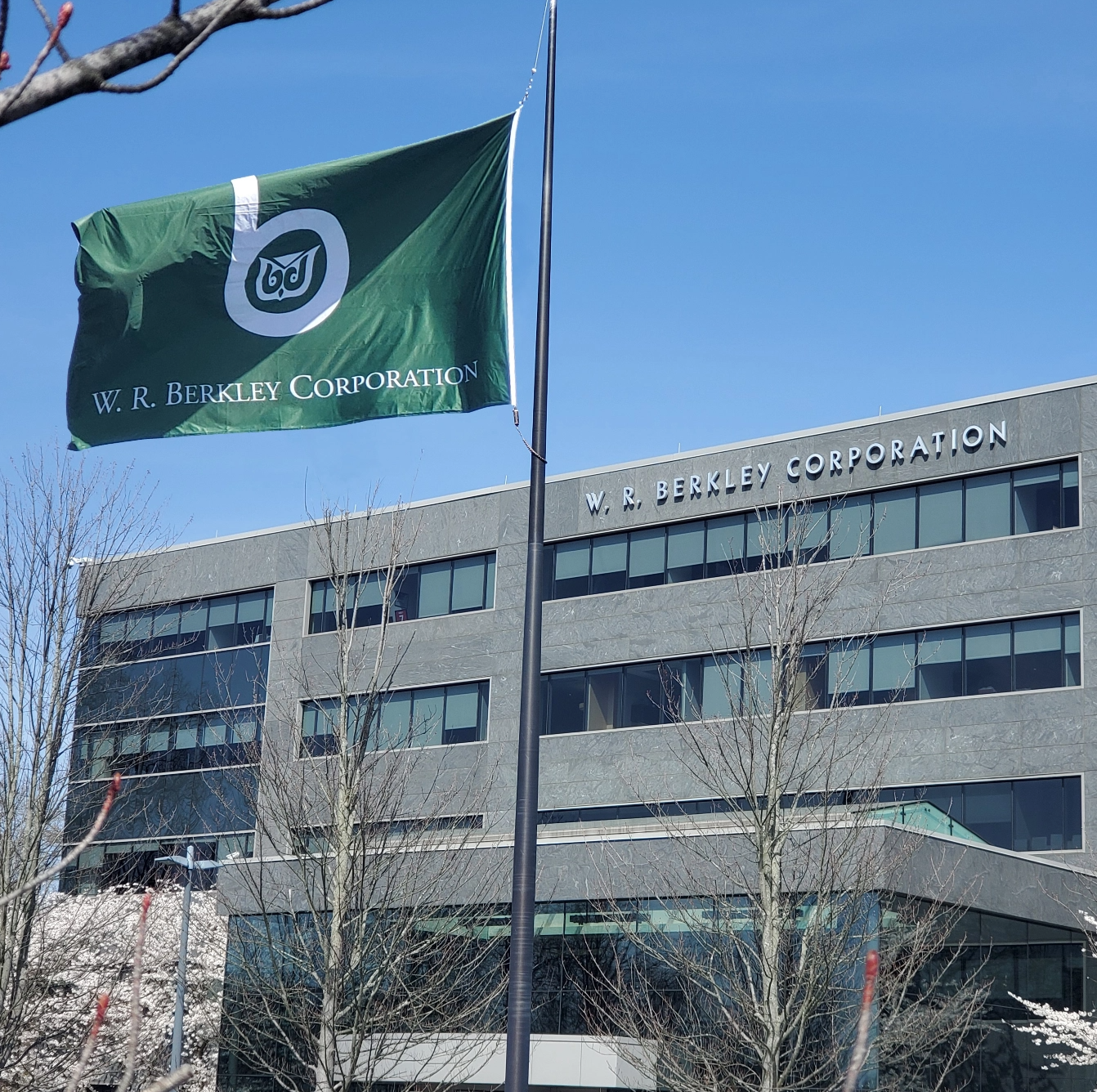
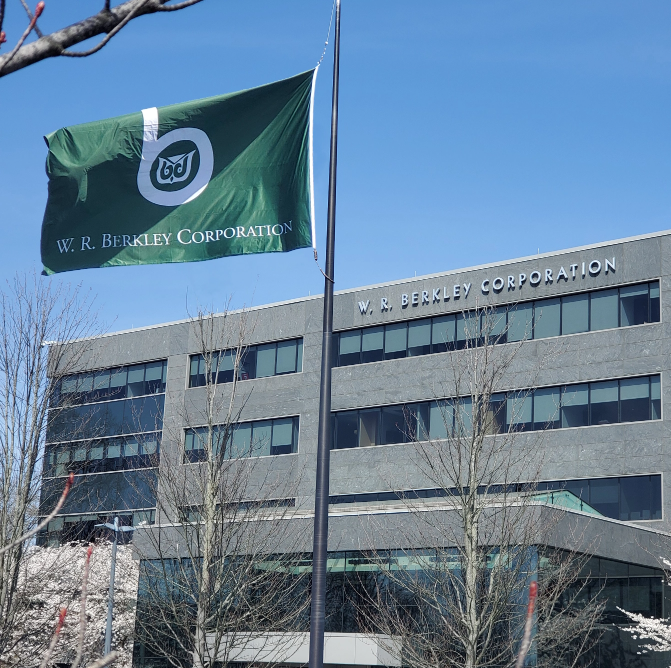
The Latest in Life Science
GLP-1 Medications – FDA Guidance and Compounded Products
Not long ago, few outside the medical community had heard of semaglutide and tirzepatide—two drugs in the GLP-1 (glucagon-like peptide-1) receptor agonist class, approved for diabetes management. The medications work by decreasing caloric intake through mimicking the natural hormone GLP-1 normally released in the gut after eating. The GLP-1 agonists bind to receptors in the brain, pancreas and intestines, which helps to regulate insulin release, lower blood sugar levels, slow down digestion, and reduce appetite.
Fluoride in Drinking Water: 2025 and Beyond
In 1999, the Centers for Disease Control and Prevention (CDC) recognized the fluoridation of drinking water as one of the “ten greatest public health achievements of the 20th Century.” The practice has reportedly reduced tooth decay in children by 40-70% and tooth loss in adults by 40-60%.
Biomarkers: Transforming Medicine
When Angela Haupt, a health and wellness editor at Time Magazine, had nearly two dozen vials of her blood drawn for a health startup, she received eight pages of clinical notes analyzing 105 personalized biomarkers. Did she receive valuable insights predictive of her future health, or an overload of indecipherable data? The answer is debatable. It may depend on who you ask, who is reading the information, and for what purpose. What is certain is that the use of biomarkers in the healthcare industry is expected to grow exponentially.